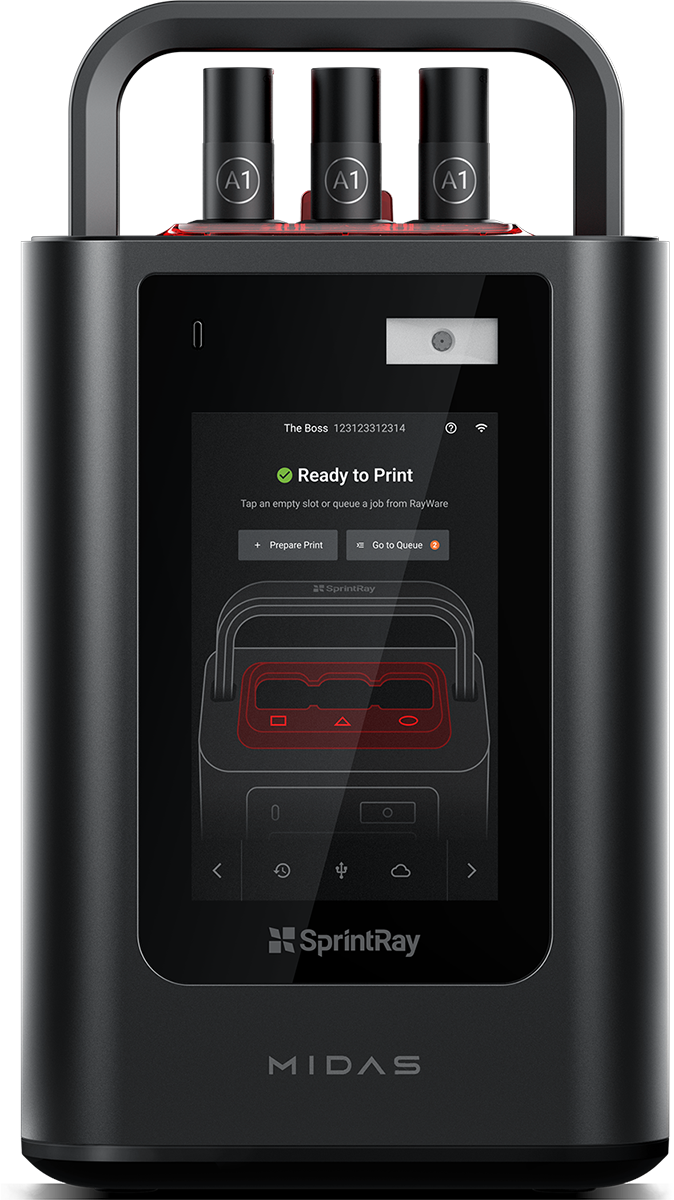
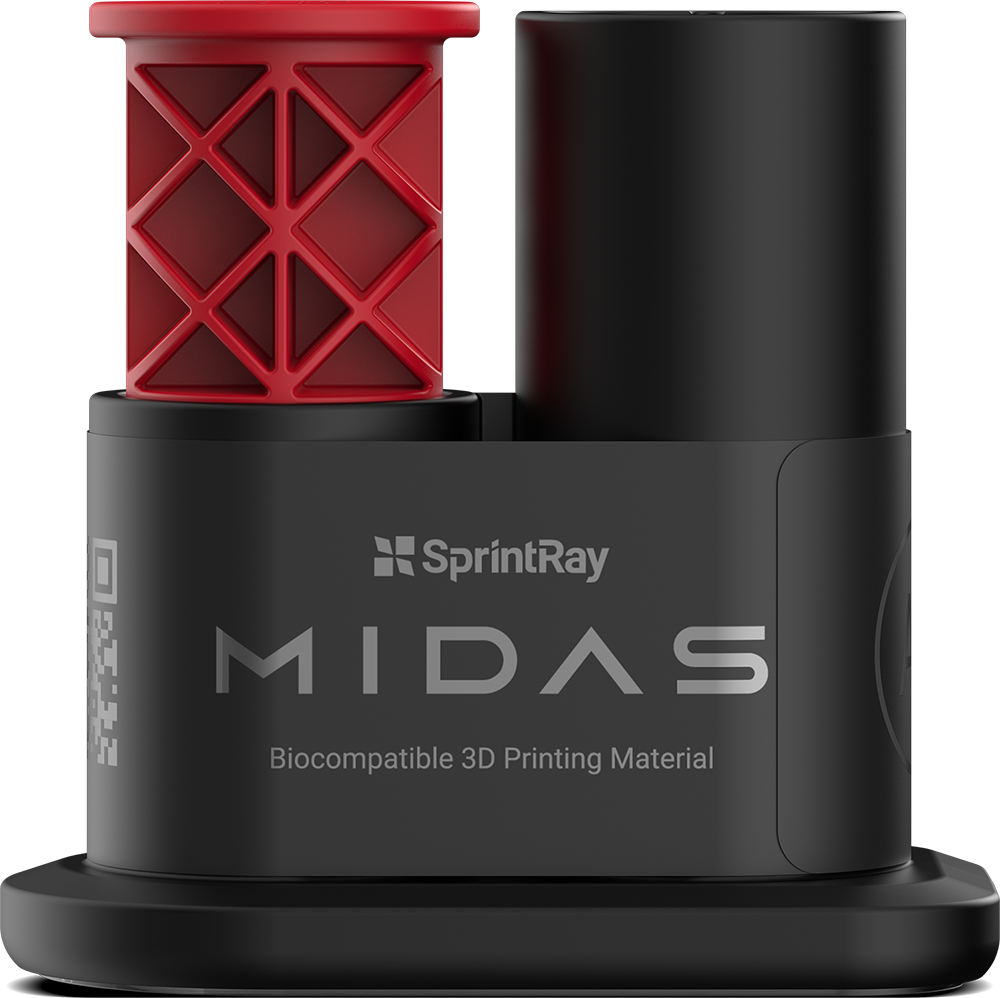


Introducing Digital Press Stereolithography (DPS)
PATENT PENDING
Midas is the ultimate solution for fabricating
chairside restorations. It uses patent-pending Digital
Press Stereolithography (DPS) to overcome the
challenges of printing highly-filled viscous
materials.
Join Waitlist
Capsule
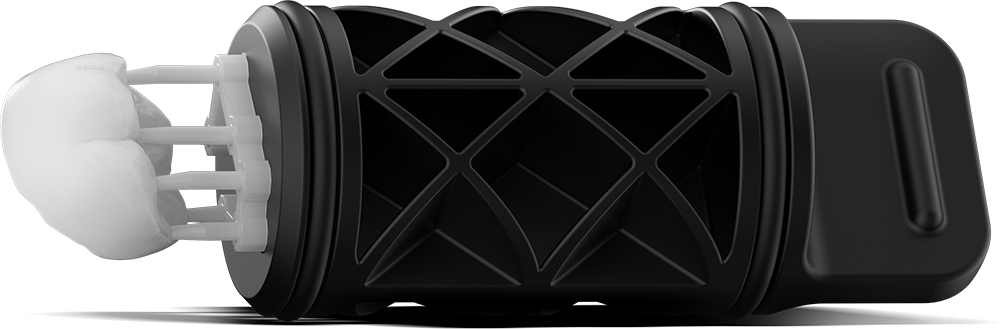
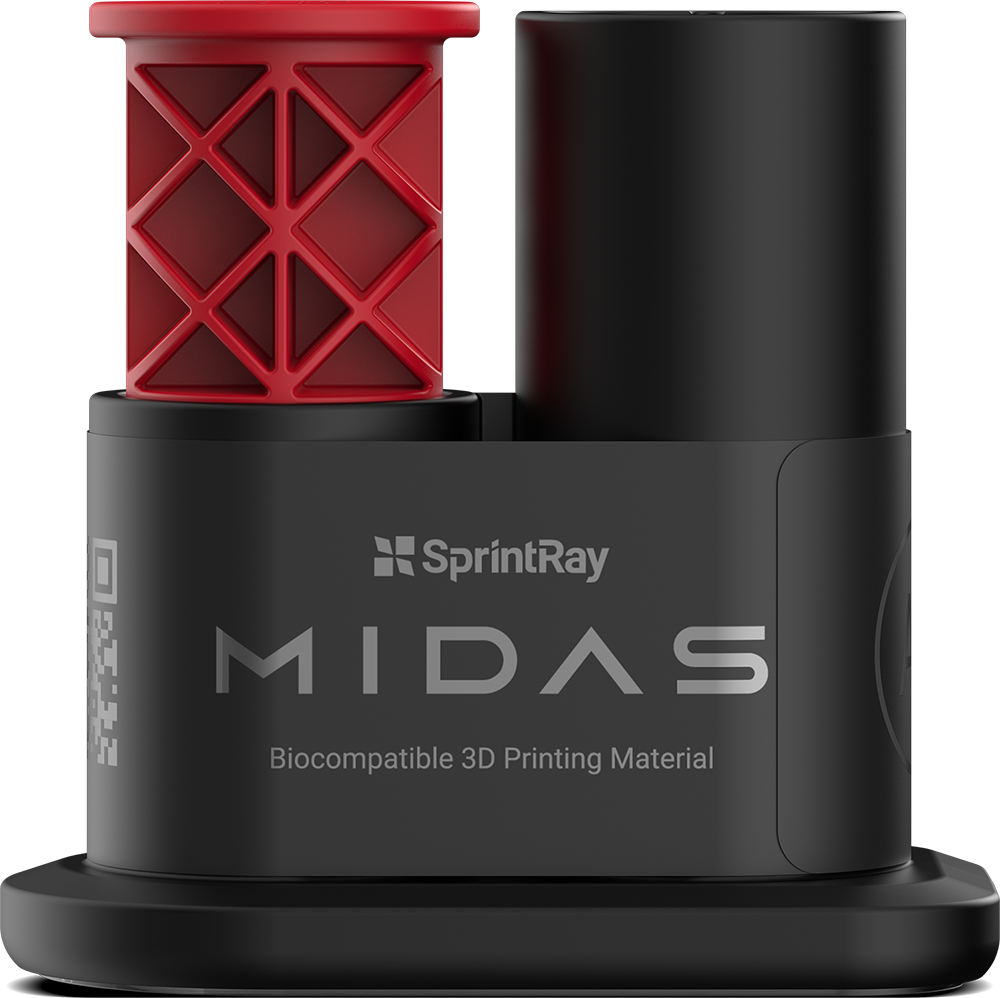
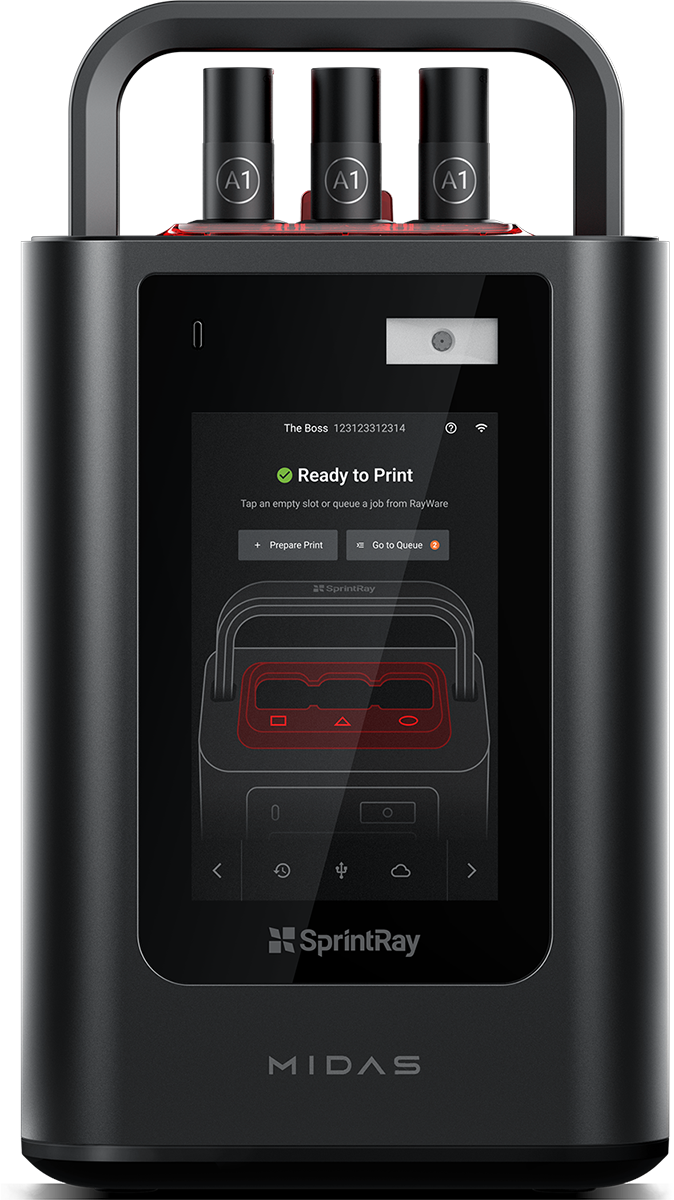
Digital Press
PATENT PENDING
Meet the New King of Chairside
The most revolutionary 3D printing tech ever to reach dentistry
What can I do with Midas?
Midas uses Digital Press Stereolithography, a
patent-pending printing method that replaces the
resin, tank, and build platform with a Resin Capsule.
This advancement allows Midas to print with highly
filled resins that are too viscous to use on a
conventional 3D printer.
No viscosity limitations
Small footprint, high output
Zero training, no upkeep
AI restoration design
Multi-restoration printing
Affordable chairside workflow
vs

Desktop Additive
Conventional 3D Printer
Conventional printers are versatile but they cannot
use highly-filled, highly-viscous restorative resins.
Multi-application workhorse
Low training and upkeep
Material viscosity limitations

Industrial Additive
Ceramic 3D Printer
Ceramic 3D printers are very expensive and require a
huge amount of space. Their workflows are very
cumbersome.
Prohibitively expensive
Huge footprint, low output
Cumbersome workflow

Subtractive
Chairside Milling Machine
Chairside mills produce great restorations, but they
are prohibitively expensive to buy and maintain.
Single restoration fabrication
Expensive to buy, costly to maintain
Large footprint, low output
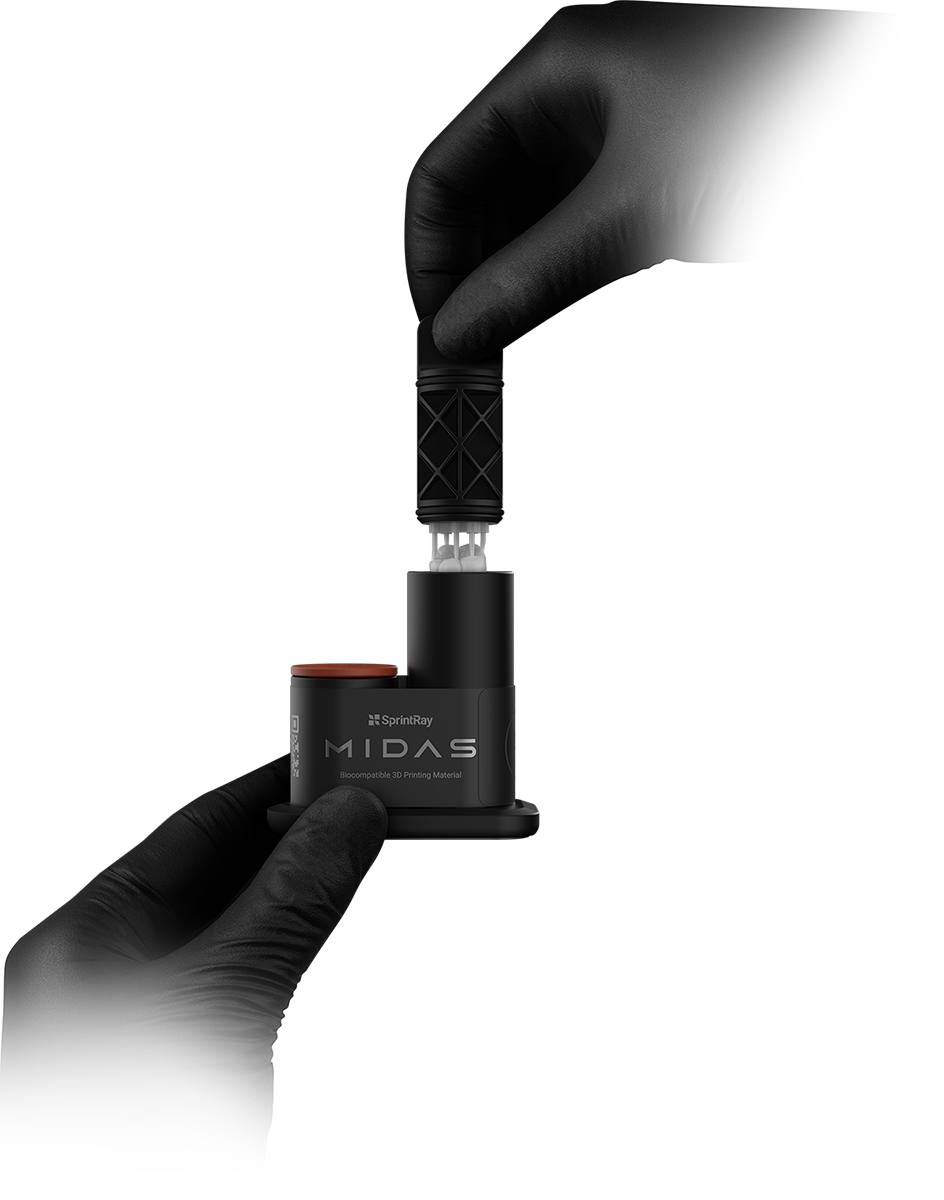
PATENT PENDING
One Capsule, Infinite Possibilities
The game changer has arrived
The Midas Resin Capsule distills the build platform,
tank, and material into a single-use item. This
innovation unlocks viscosity-agnostic 3D printing
while offering incredible speed, accuracy, and
workflow simplicity.
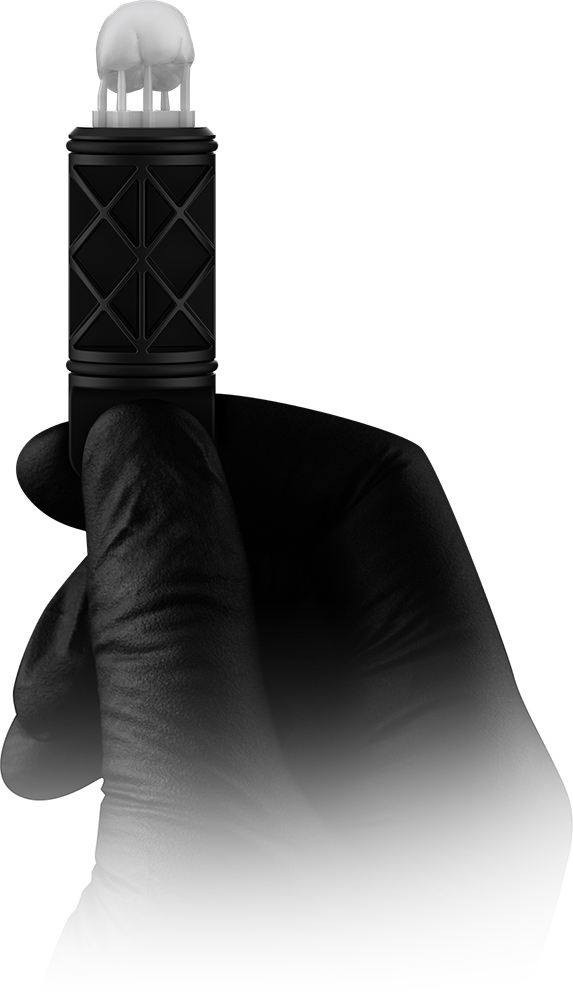
Crowns
Full contour crowns with lifelike aesthetics and
mechanicals thanks to extremely high filler content
Posterior crowns
Anterior crowns
Implant crowns
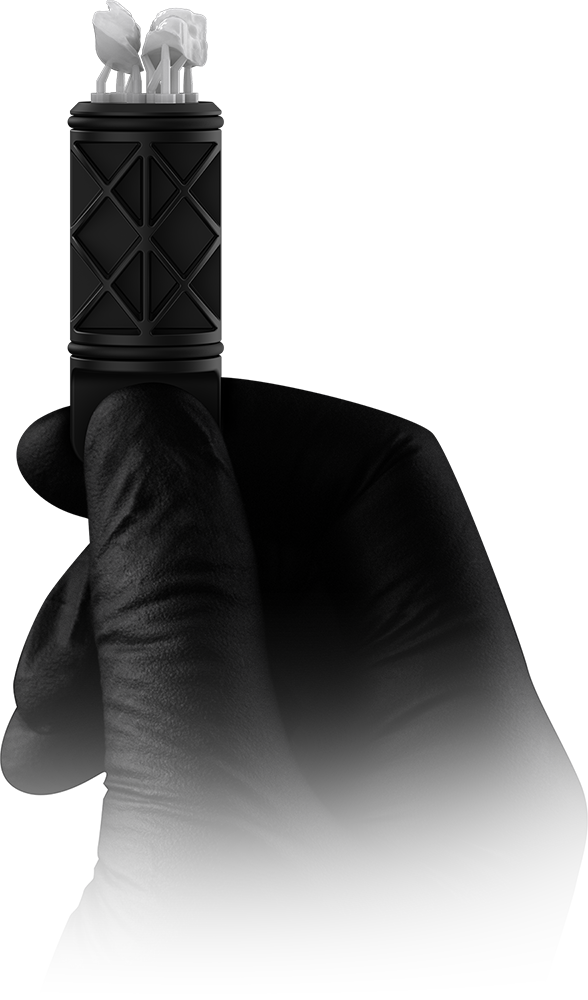
Inlay & Onlay
Complex shapes print with pixel-perfect accuracy on
Midas - fabricate up to 2 inlays per capsule
Fillings
Onlays
Inlays
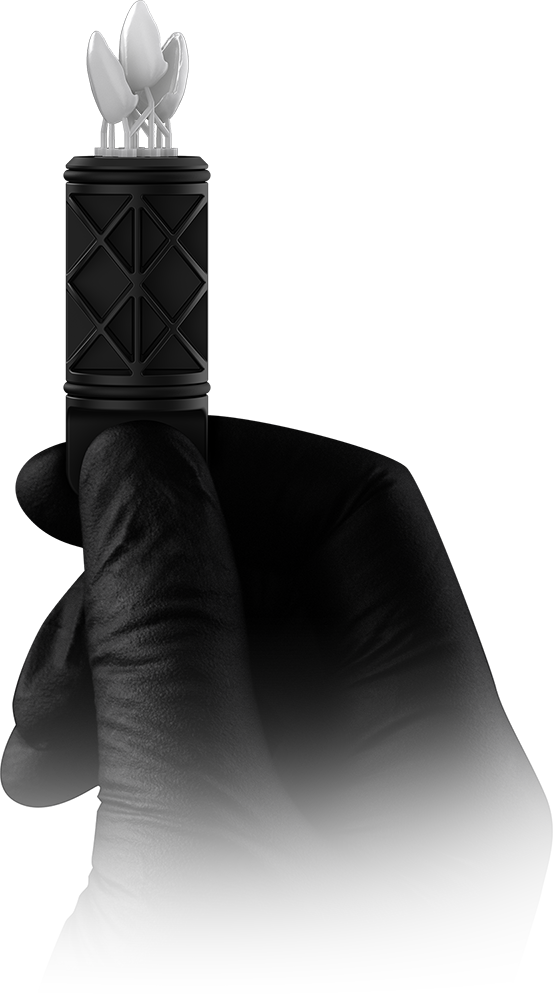
Veneers
Print up to 3 incredibly thin, strong veneers per
capsule for minimally invasive cosmetics
No-prep veneers
Prepped veneers
Scan. Place. Press.
The easiest way to fabricate chairside restorations
Anyone can print a restoration on Midas. Because it
uses resin capsules rather than cumbersome bottles and
tanks, printing is as simple as making your morning
cup of coffee.
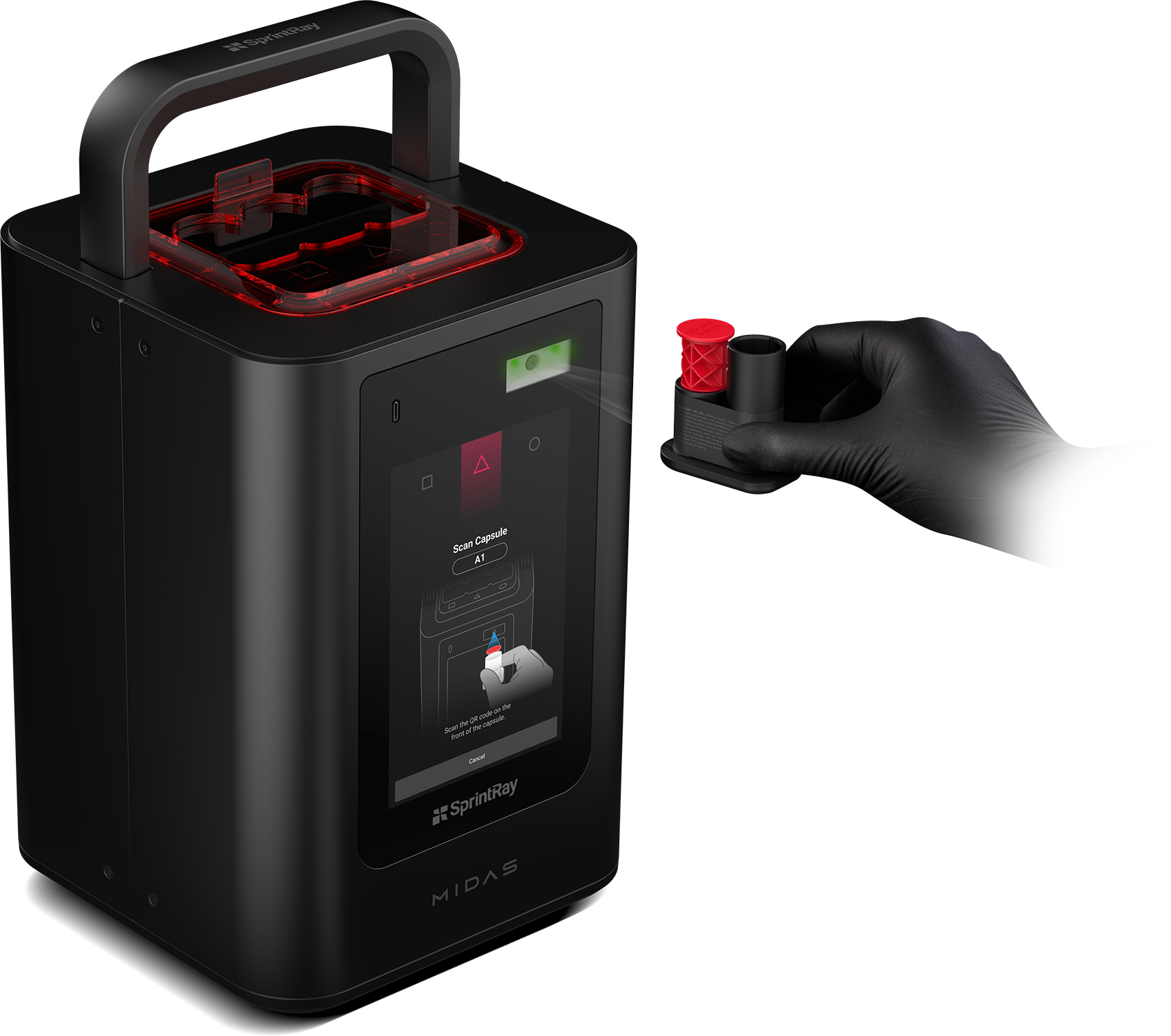
Step 1
Scan
Every Midas Capsule is coded with its material type,
shade, manufacturing information, and expiration date.
When it’s time to print, simply scan the capsule using
the barcode Scanner.
Automatic medical device tracking
Resin and shade detection
Robust error proofing
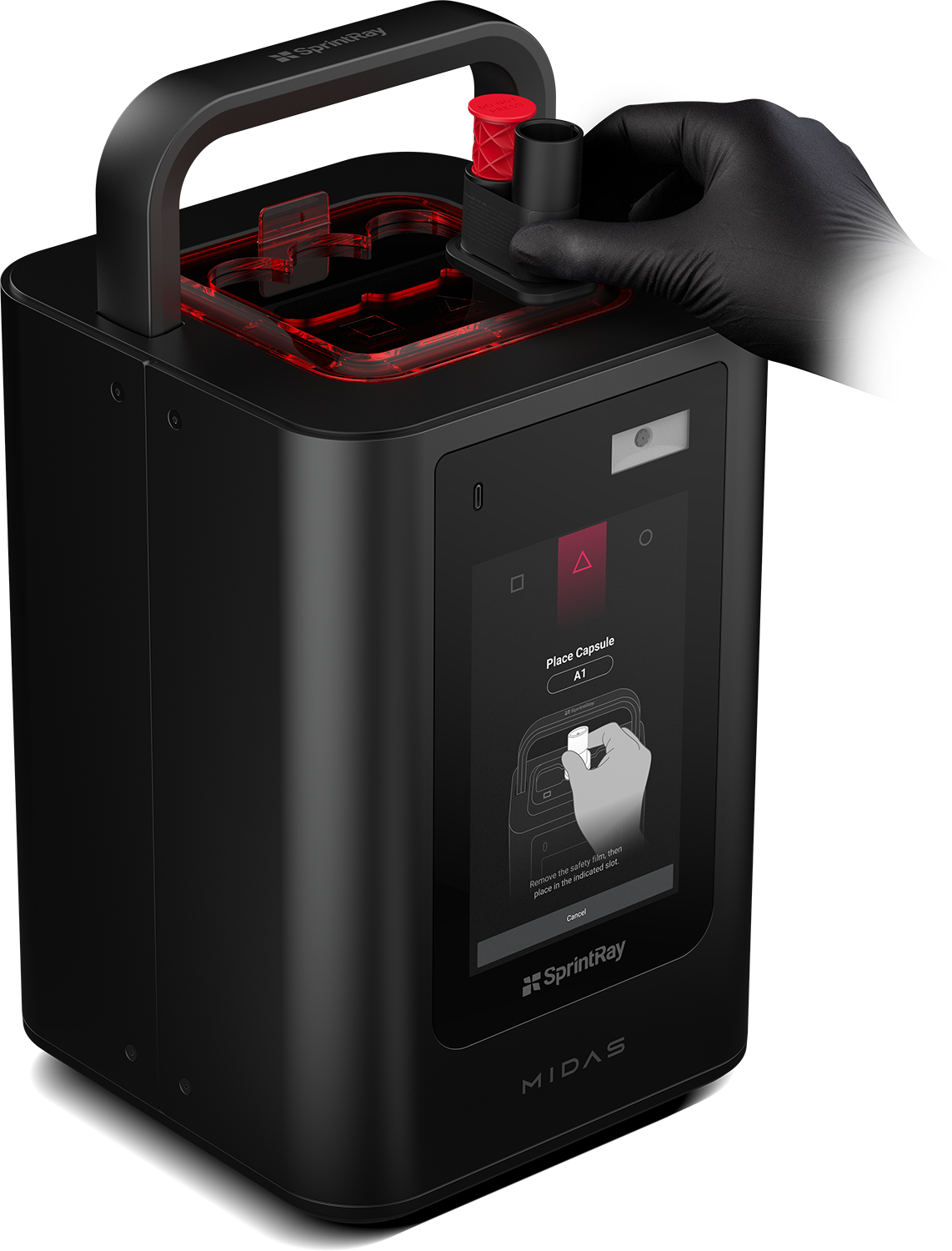
Step 2
Place
Midas has three printing slots on the heated print
glass. After scanning, the onboard computer will tell
you where to place the cartridge.
Print up to 3 capsules at once
Capsule placement detection
Fully guided workflow
Applications
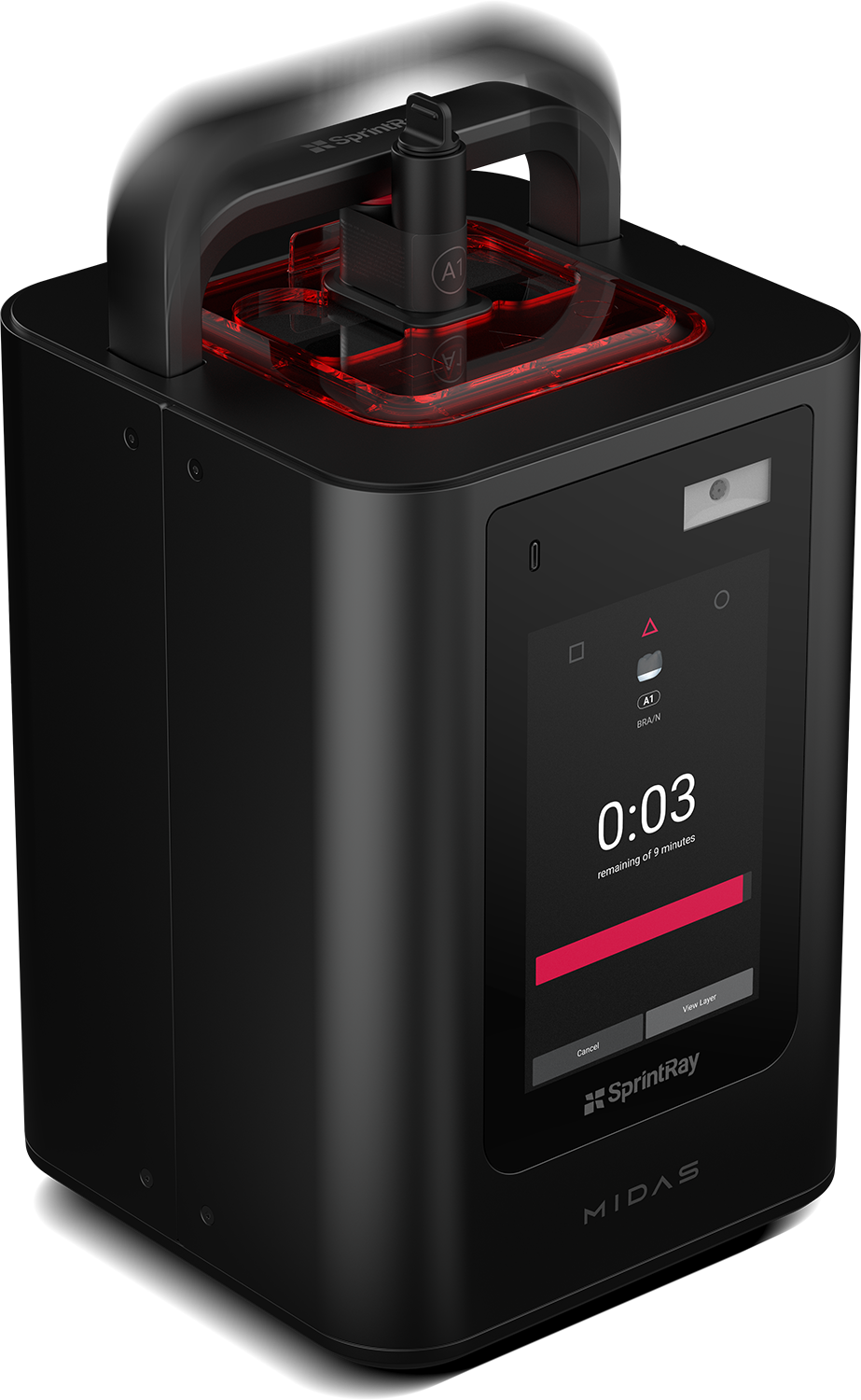
Step 3
Press
Midas will start pressing once you’ve scanned and
placed all the capsules for a print job. The print
loop will slowly lower while the resin is cured.
Print in less than 9 minutes
Mess-free workflow
DPS Explained
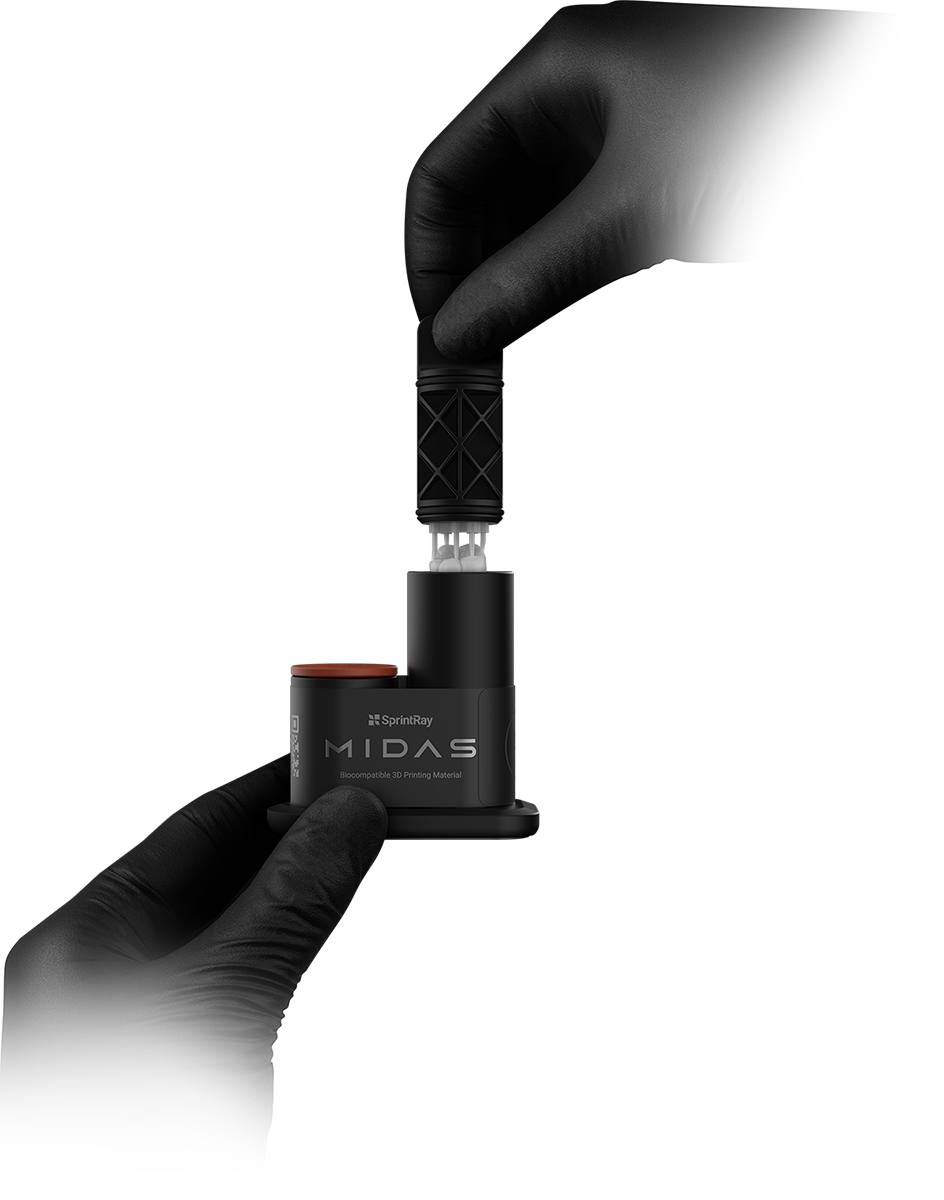
Step 4
Remove Print
Remove the capsule from the print glass. Pull the tab
on the build platform to remove it from the capsule.
Your restoration is ready for post processing.
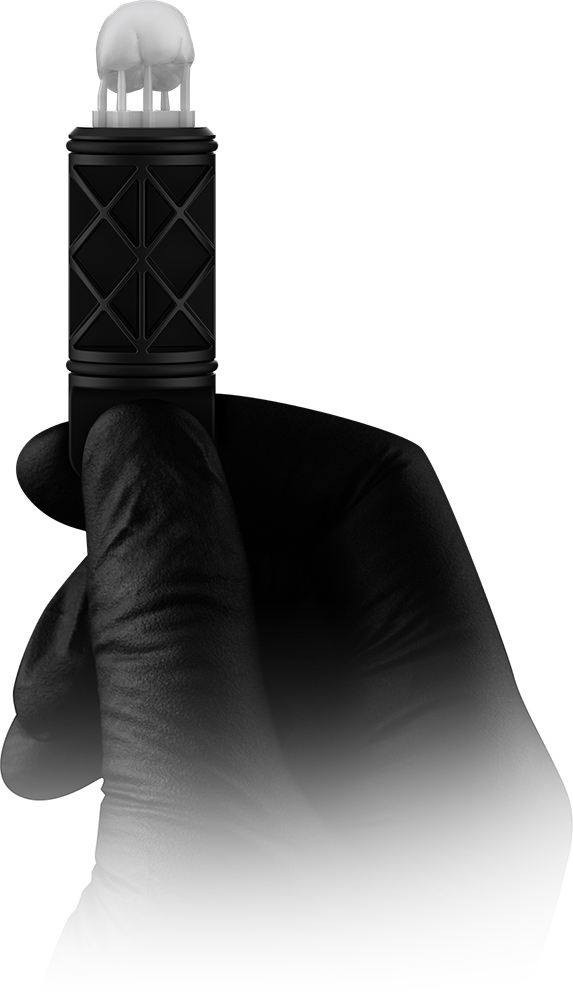
Hop, Step, and a Quantum Leap
Now, you can place ceramic composite restorations
quickly and at a fraction of the cost. Welcome to the
future. Welcome to Midas.
DPS Explained
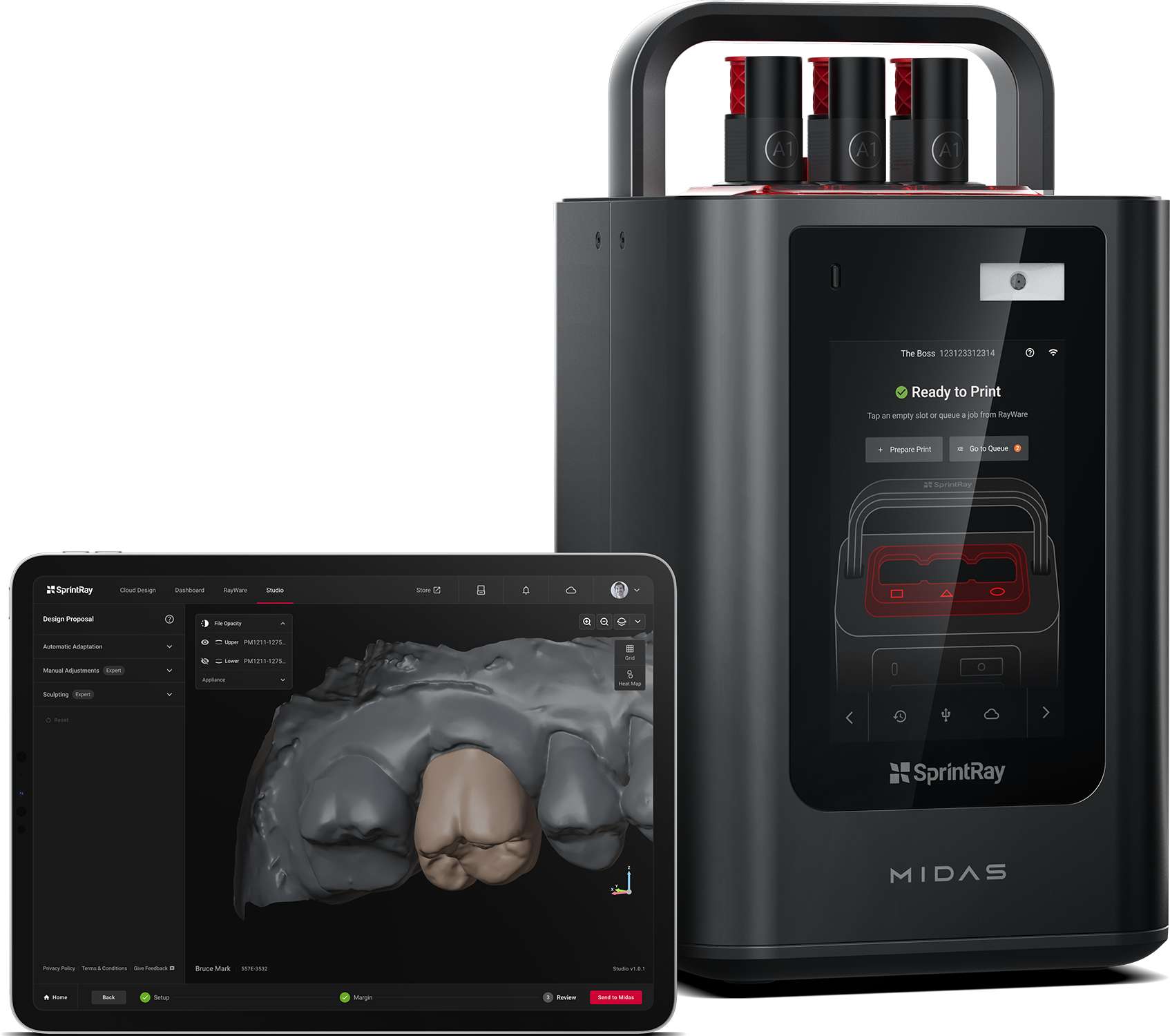
Easy Design Workflow
AI-assisted Midas Design Studio generates restorations in moments
AI Studio combines the convenience of AI design with
the versatility of CAD to create a simple, cloud-based
design suite. Designing a restoration with Studio is
easy for anyone, while customization options like
margin and adaptation adjustments help create a
perfect fit.
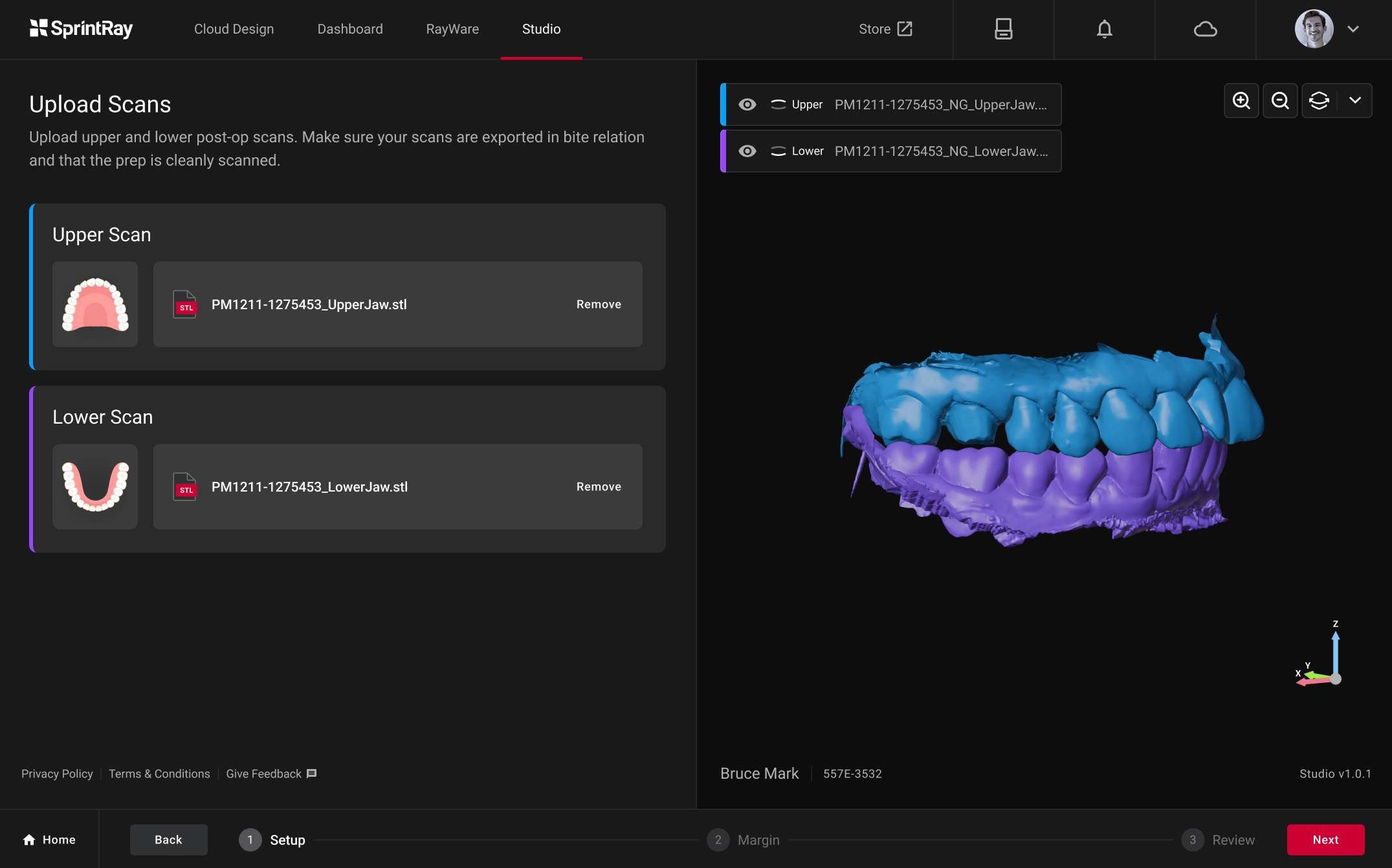
Step 1
Upload Scans
AI Studio takes upper and lower post-op scans
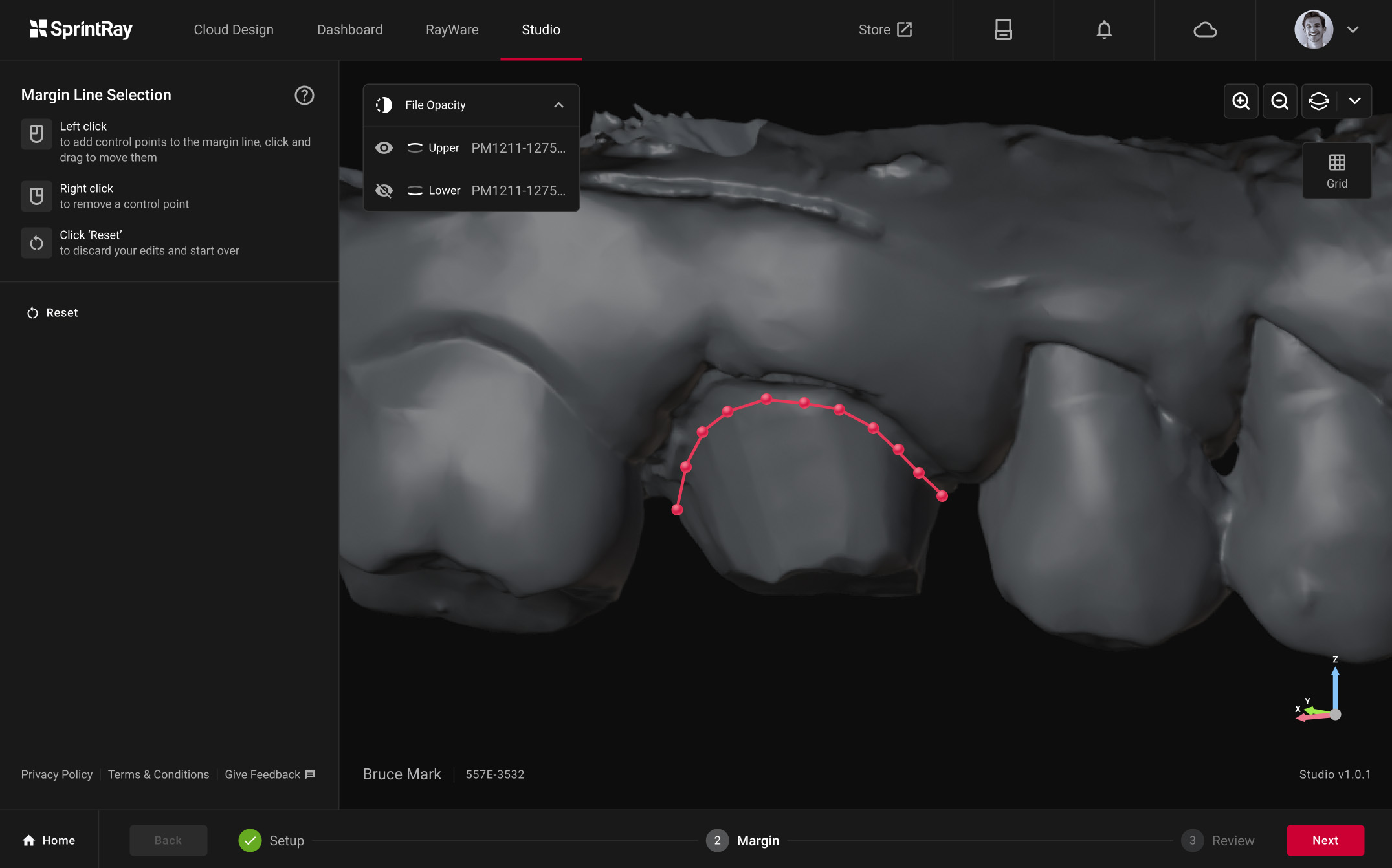
Step 2
Confirm Margin
Adjust the automatic margin line to get the perfect
crown
Automatic margin detection
Margin editing

Step 3
Final Touches
Adjust the aesthetics and final positioning
Automatic adaptation
Manual positioning
Anatomical sculpting
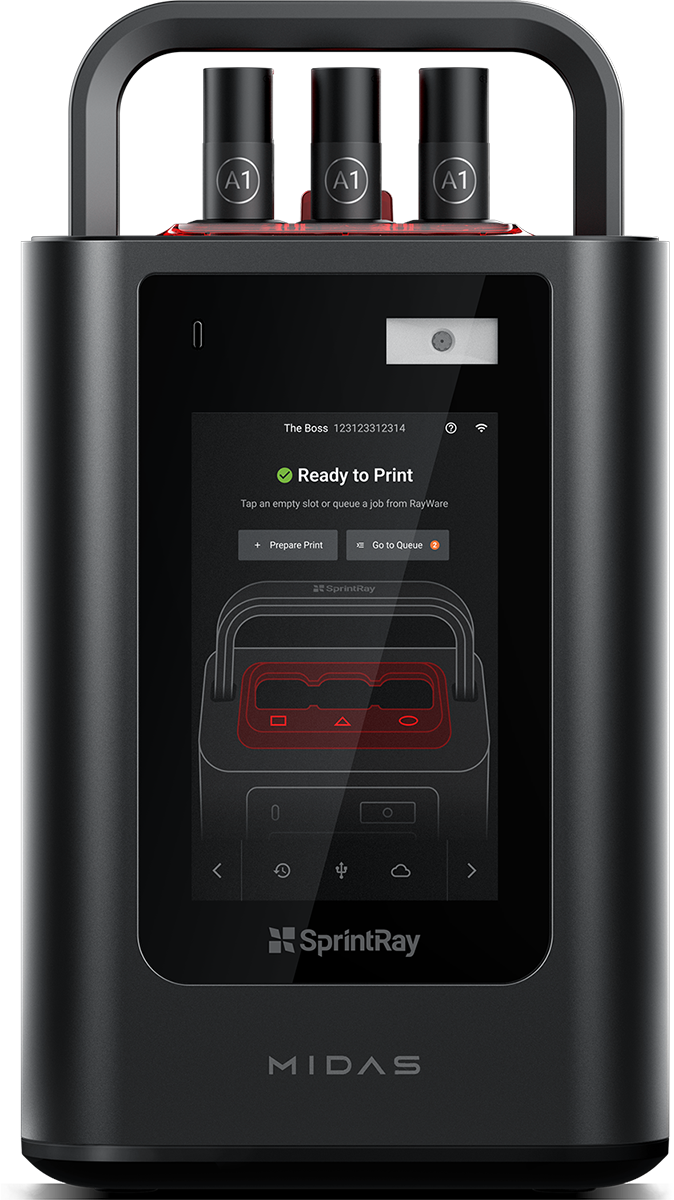
Step 4
Print on Midas
Send your crown design directly to Midas to print in
under 10 minutes - now that's chairside service
See Workflow
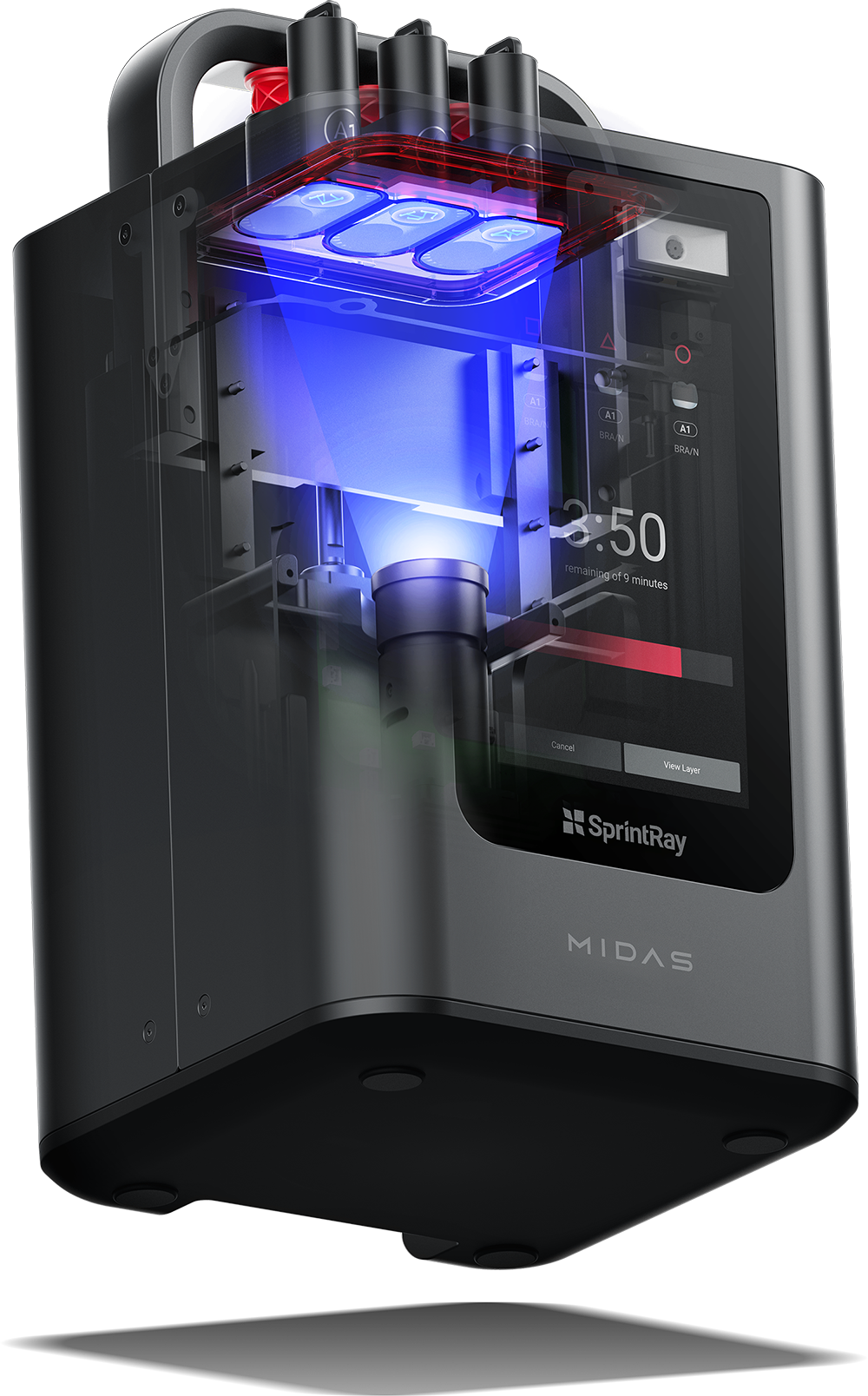
Every Considered Detail
Engineered for precision, designed for your workflow
To build a product as revolutionary as Midas, we left
no stone unturned. From its thoughtful size and
proportions to the materials used in manufacturing, we
pulled out every stop to bring Digital Press
Stereolithography to your office.

Unparalleled Accuracy
Midas delivers harmony between hardware, software, and
workflow. Using a capsule to deliver resin doses
eliminates variability from the workflow. Combined
with direct projection and 385 nm light, Midas
provides outstanding precision.

385 nm Light
Midas uses 385 nm UV-A light for incredible depth of
cure control, improving print quality today and resin
development tomorrow. This innovation leads to better
surface finish, improved layer accuracy, and enhanced
fit and finish for pixel-perfect restorations.

Incredibly Compact
Midas is extremely compact because it doesn't need to
hold a large tank of liquid resin or a permanent build
platform. Midas can be placed almost anywhere it fits
- because the resin is stored in sealed capsules, it's
less sensitive than a conventional 3D printer.

45 µm Direct Projection
Midas uses a 45 µm projector to directly deliver light
to the print glass with minimal distortion and
superior precision. Mounting the projector this way
simplifies the optical path and removes the need for
light reflection, drastically improving accuracy.
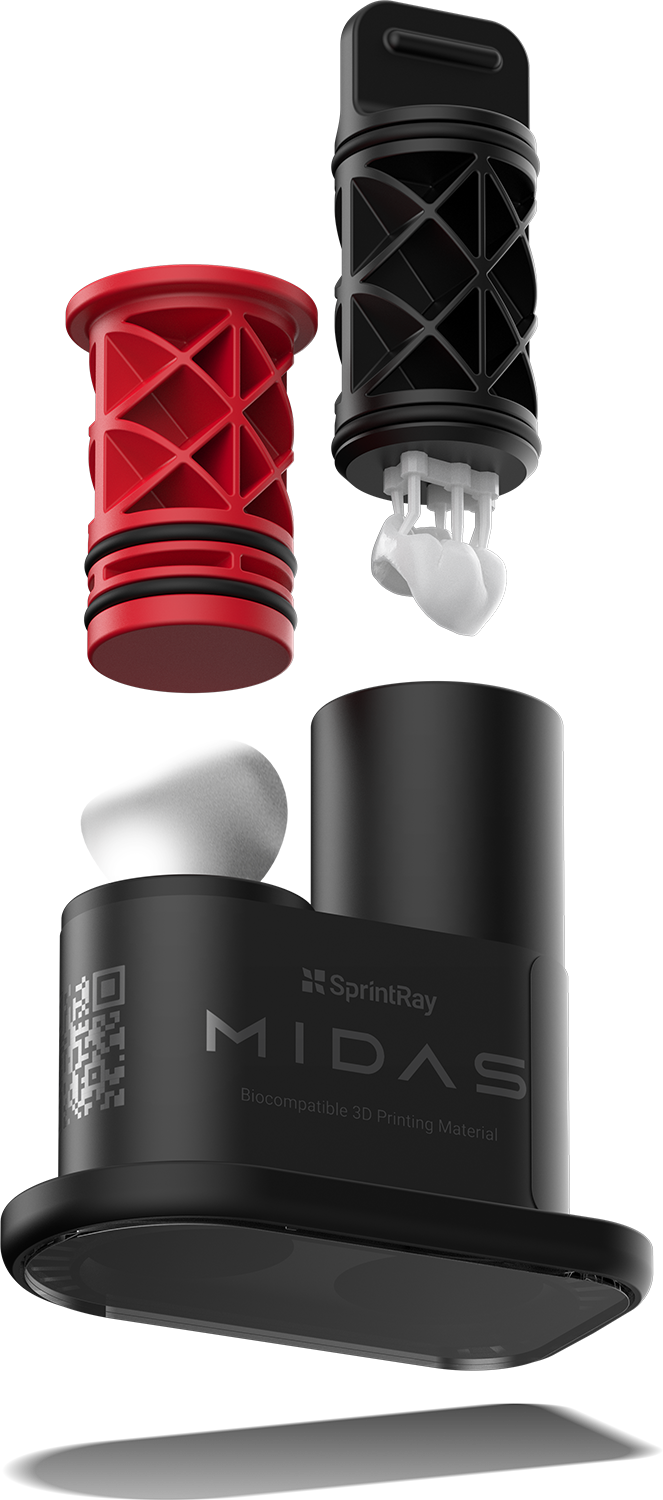
PATENT PENDING
Workflow Nirvana
Simplicity unlike any other 3D printer
Resin capsule technology supercharges the best
workflow in dentistry. There is no more exposed resin,
resin tanks, or build platforms. Midas makes it
simple.
How it Works

Zero Maintenance
Ready for your maintenance checkup? Wipe down the
print glass. Seriously - that’s it. No resin tanks, no
build platforms, just place and print.

Training-free Workflow
Scan, place, print. The workflow for Midas is really
that simple: scan each cartridge and instructing you
where to place it. It’s error-free and requires no
training.

Medical Device Tracking
The onboard QR code scanner helps simplify the
workflow, but it also provides medical device tracking
for expiration dates, lot numbers, and more.
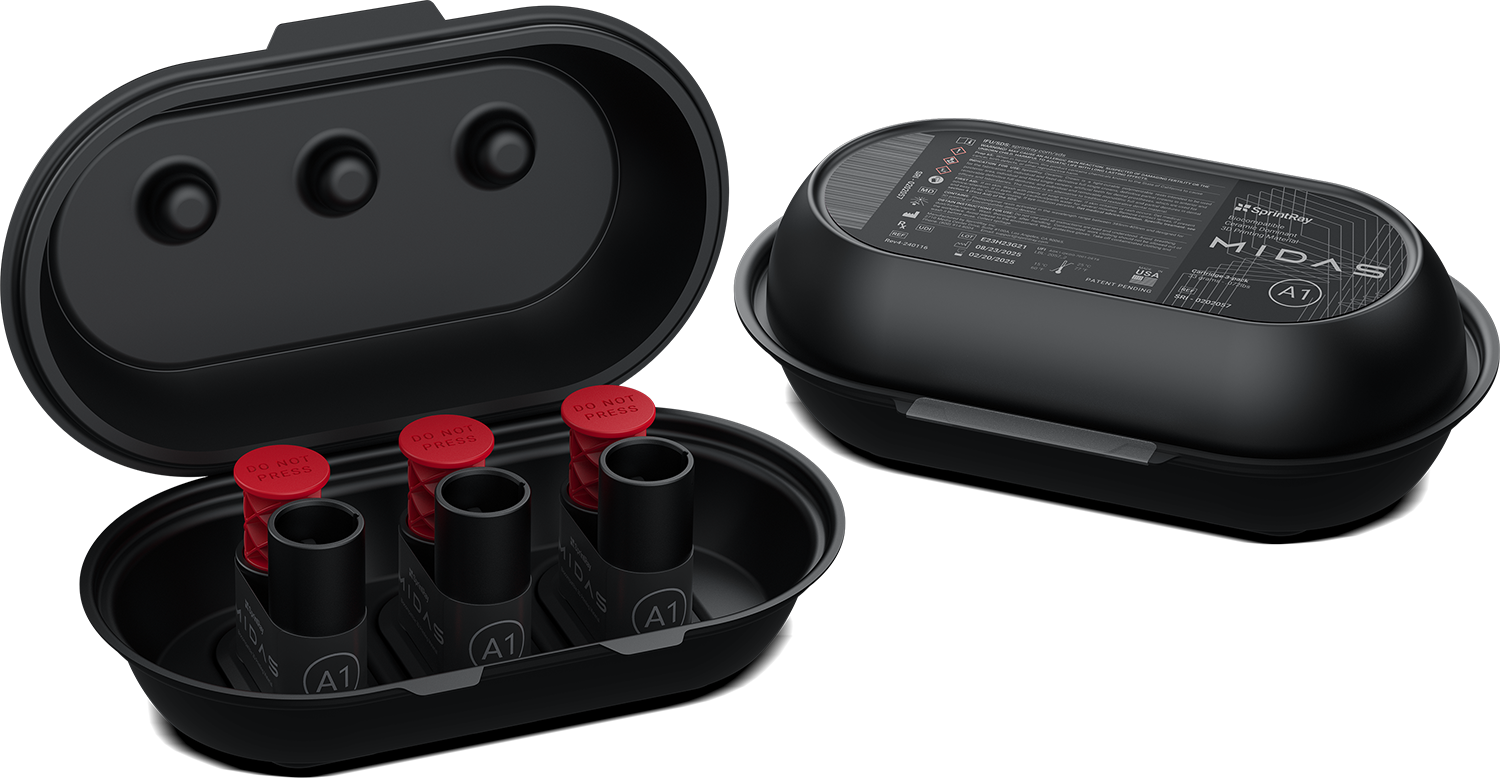

Simplified Resin Handling
Midas Capsules come in sets of three so you can easily
stock multiple shades and resin types. The included
storage container protects them from the elements.
It's also stackable, for simplified inventory
management.
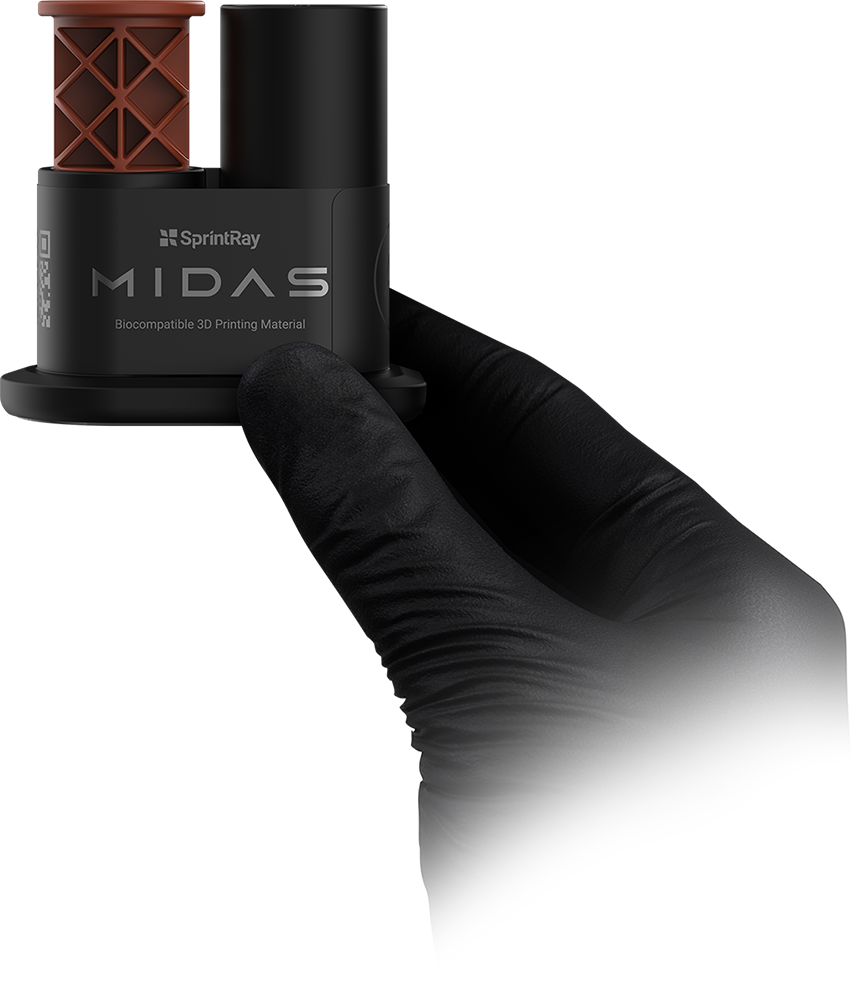
PATENT PENDING
Digital Press Stereolithography (DPS)
A patent-pending technology by SprintRay
Digital press stereolithography (DPS) 3D printing uses
hydrodynamic principles to create an environment where
the viscosity of the resin is no longer a barrier to
speed or accuracy. This technology allows Midas to
print up to 3 definitive crowns in 10 minutes,
regardless of filler content.

Viscosity Agnostic
A material's physicality does not bind Midas — DPS
uses hydrodynamic principles to move material through
the stereolithography process.

Space Saver
Midas uses a highly compact design to deliver an
incredible size-to-performance ratio. You can fit it
almost anywhere due to its small footprint.

Just Getting Started
DPS is the start of a new era of 3D printing. It
simplifies the workflow and opens the door to a whole
new world of biomaterial innovations.
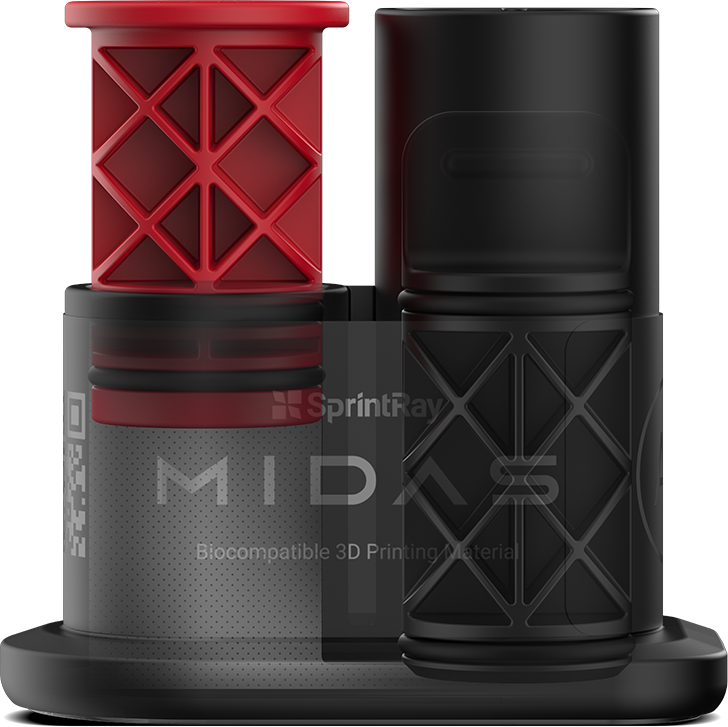
Before Pressing
Viscous material sits in the pressurized resin
chamber. The build platform is tucked into the build
cylinder.
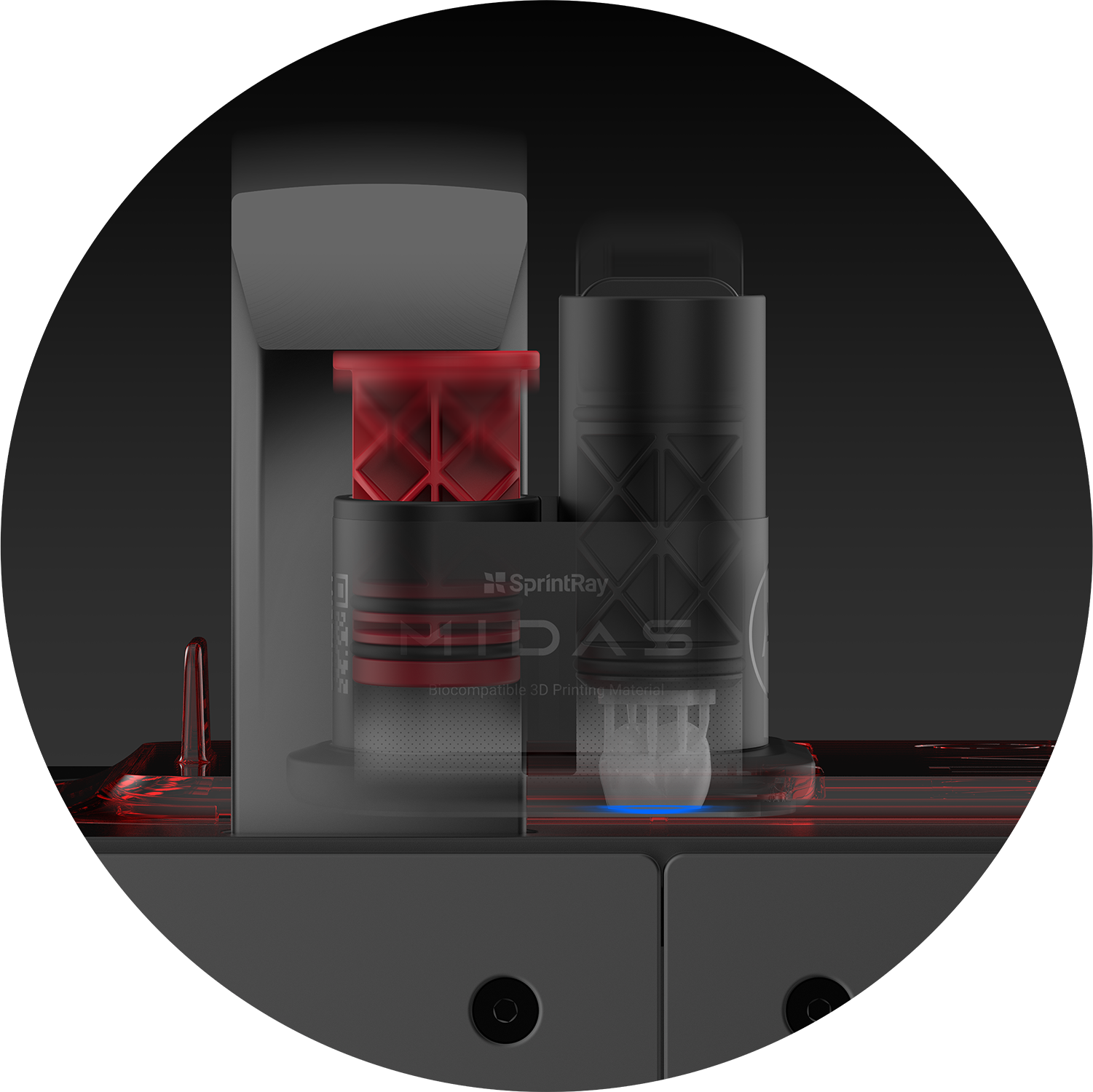
while pressing
The material is pressed and dispensed into the build
area. Hydrodynamic principles push the build platform
up as it cures.
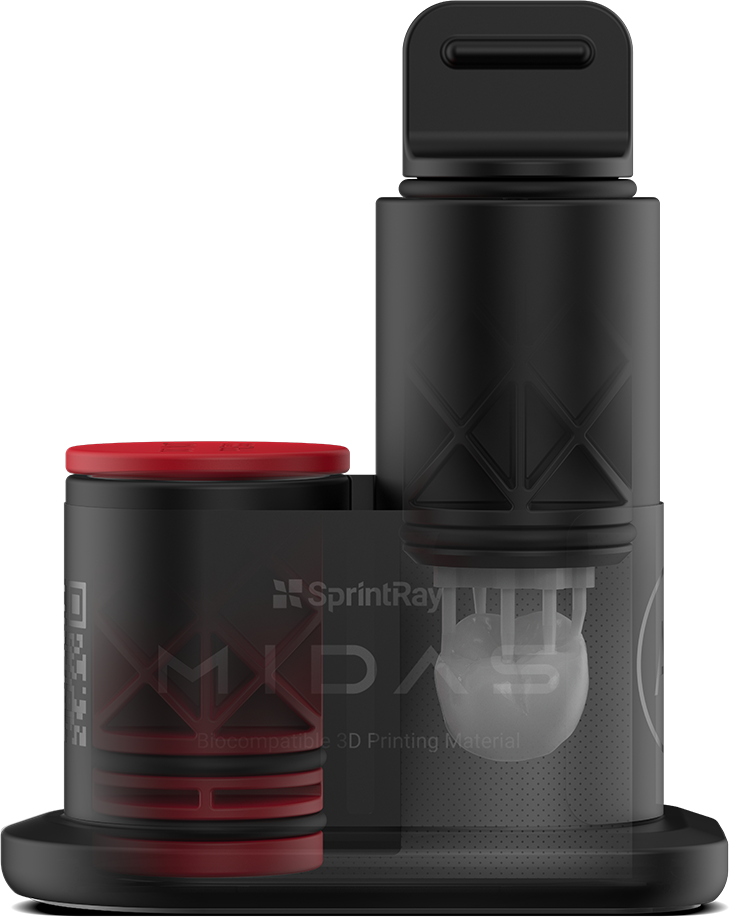
After pressing
When the pressing is finished, the build platform is
ready for extraction along with your printed
restoration.
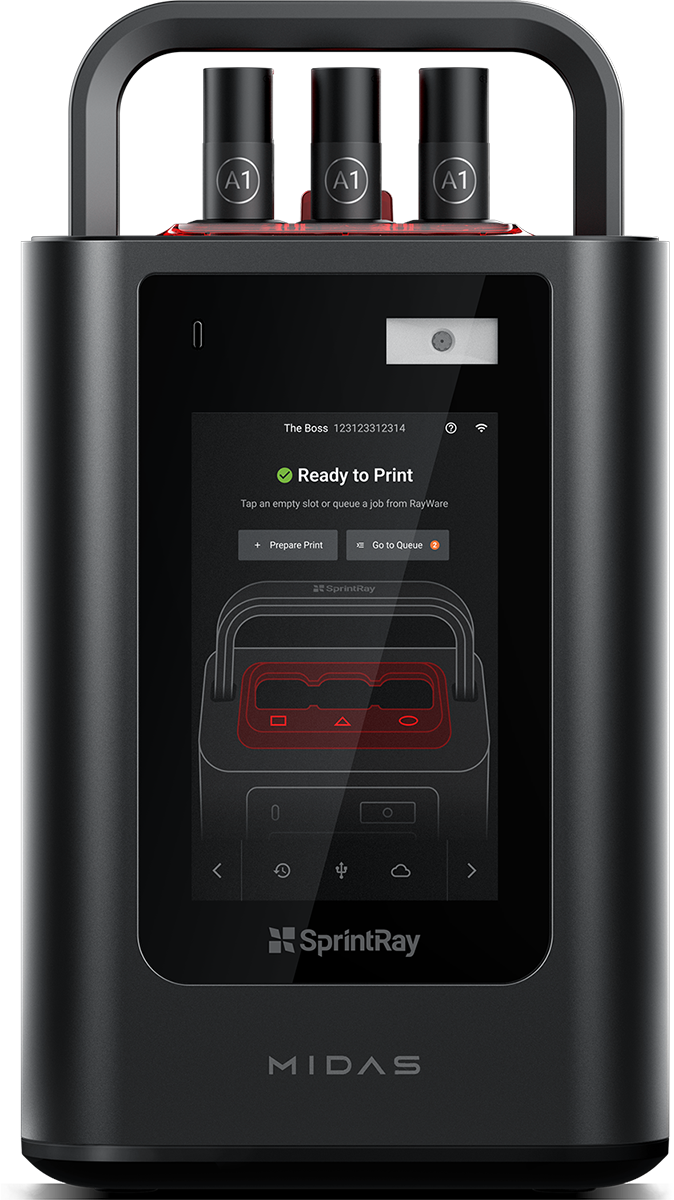
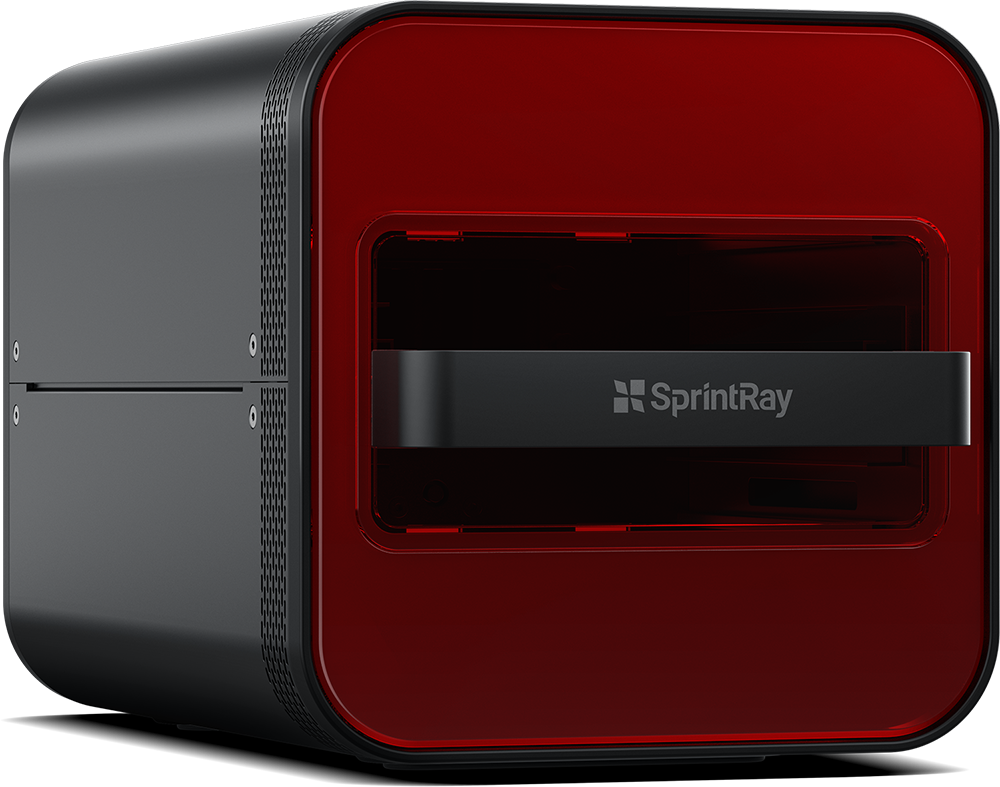
Perfect Pair
Midas and NanoCure are better together
Midas and NanoCure help you deliver definitive
restorations with outstanding speed, accuracy, and
mechanical properties. These compact, advanced devices
can help any office upgrade from outsourcing to
chairside care for a fraction of the cost of a mill.
See NanoCure

Supa-fast Workflow
Design, print, and post cure a definitive crown in
less than 30 minutes.

Compact Ecosystem
Midas and NanoCure together take up less space than a
typical milling machine.

Unlock the Future
With DPS and dual-wavelength curing, your office is
ready for the future of biomaterial innovation.
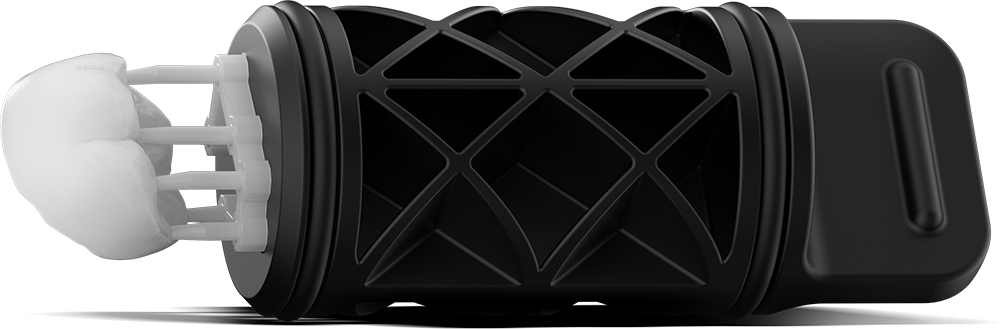
Enter a New Era
Reserve your spot for the future of dentistry
Making a restoration on Midas is like magic. It marks
the beginning of a new era where highly-filled
composite restorations can be designed and fabricated
chairside in minutes. A future where dental care is
more economical, responsive, and customizable .
Join the waitlist now to experience a new era of dentistry.
Join the waitlist now to experience a new era of dentistry.
Join Waitlist
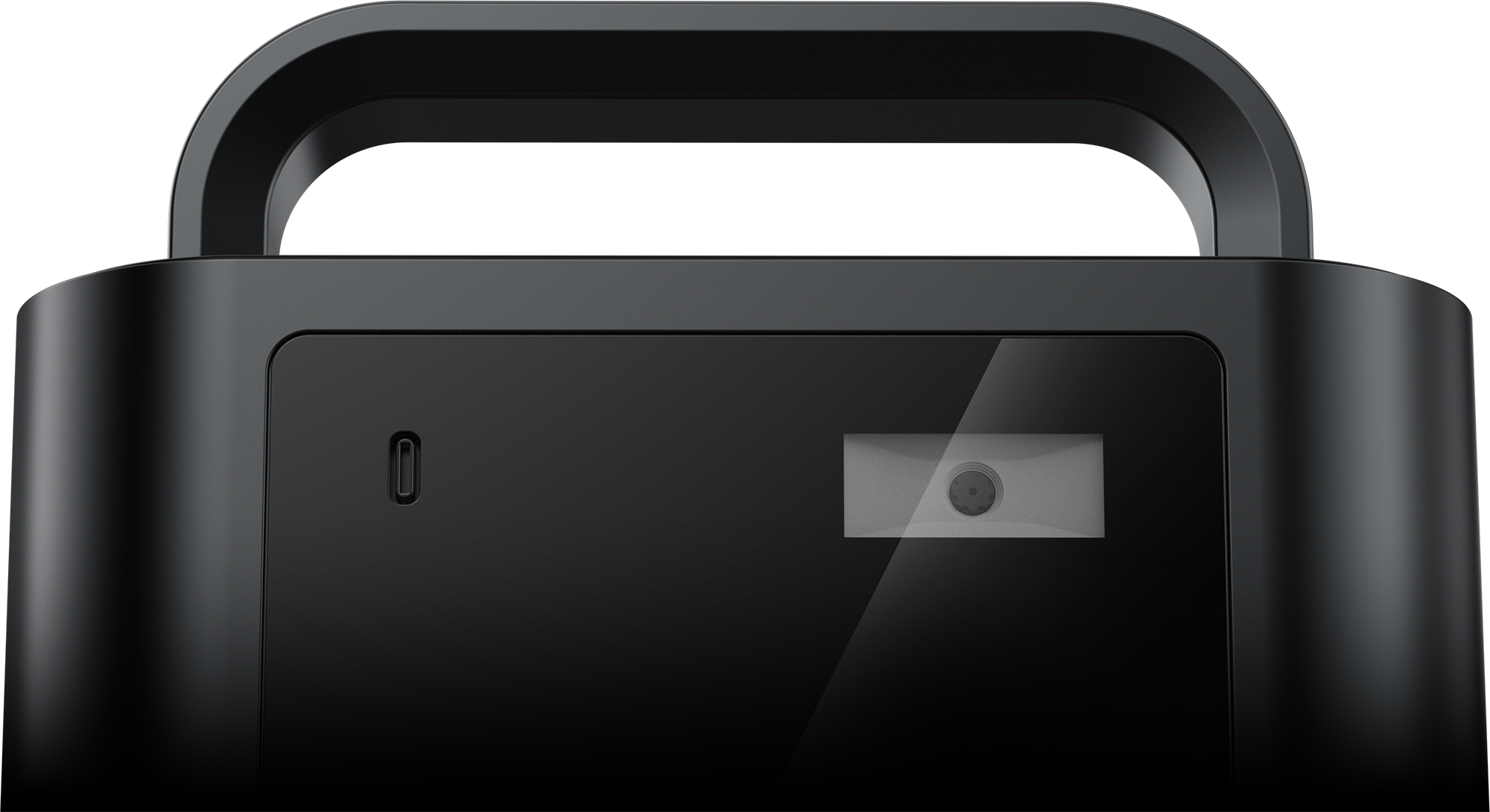